Spotlight on Off-Road Transportation Electrification: Turner Construction Company’s Meta Project
November 21, 2023 | M. Moaz Uddin | Environment
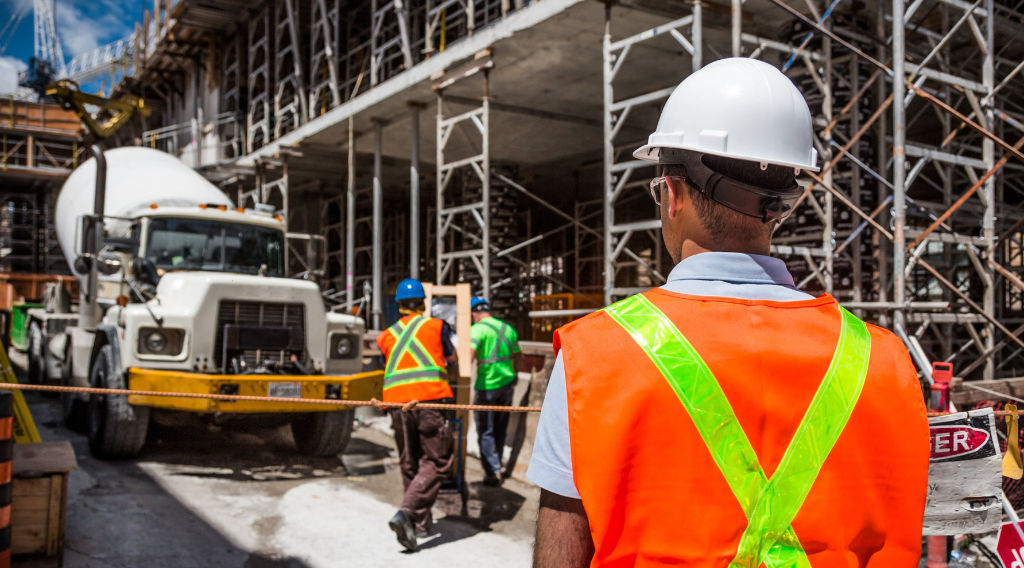
While we often hear about the electrification of passenger vehicle fleets and, more recently, commercial vehicle fleets, off-road transportation is often sidelined in these conversations. This post is part of a series that will spotlight electrification efforts for off-road vehicles, which include equipment and machinery used in construction, mining, agriculture, and ports.
According to the United Nations Environment Programme, the buildings and construction industry is responsible for 37 percent of global energy and process-related carbon dioxide emissions. Off-road vehicles are also significant sources of air pollution, accounting for almost three-quarters of the fine particulate matter (PM2.5) and one-quarter of the nitrogen oxide (NOX) emissions from mobile sources.
Hybrid and electric construction equipment allow construction companies to lower project emissions.
Like hybrid passenger vehicles, hybrid construction equipment incorporates batteries and motors with an internal combustion engine to improve powertrain efficiency. In addition to being charged by the internal combustion engine, the batteries are also replenished by regenerative charging from dropping loads, lowering the boom, and other movements that capture kinetic energy.
Electric construction equipment uses electricity as its primary power source to operate various components and perform construction tasks. Some electric equipment can be directly connected to a power source through a cable or plug. Still, most bigger machines have lithium-ion battery packs that store electrical energy.
When we discovered that Turner Construction Company—the largest construction company in the US by revenue, employing 10,000 people—is piloting electric and hybrid construction equipment on a project with Meta, we wanted to learn more about it. We had the opportunity to interview Mike Bahr, sustainability manager at Turner Construction Company, to discuss electric and hybrid construction equipment deployment at the Meta data center project.
Q1: Can you tell us about the Meta data center construction project in Altoona, Iowa? How did Turner Construction Company pivot to hybrid and electric construction equipment?
The Altoona data center is one of Meta’s largest data centers in the world, comprising over 5 million square feet of space.
The Meta data center project in Altoona, Iowa, represents a decade-long partnership between Meta and Turner Construction Company, driven by a shared commitment to sustainability. Both companies have prioritized emissions data reporting within their supply chains, making this partnership a natural fit.
The data centers built for Meta serve critical functions in data storage, artificial intelligence programming, and the Metaverse.
Turner Construction Company helped found the United States Green Building Council, which developed the LEED [Leadership in Energy and Environmental Design] certification for buildings. In 2019, the company started tracking on-site emissions. Since then, the company has set targets for net-zero emissions in its operations by 2030 and across its entire supply chain by 2040.
Turner Construction Company joined forces with Sunbelt Rentals to test hybrid and electric construction equipment at this site, marking a significant step toward greener construction practices.
Q2: How are you cutting greenhouse gas emissions at this site? Have you quantified the emissions reductions on sites that have hybrid and electric construction equipment?
The Meta project is massive, employing a wide variety of construction equipment and practices. We brought hybrid and electric equipment to this site and ran alongside conventional equipment to evaluate performance, fuel usage, emissions, and noise reduction. In addition to analyzing these quantifiable variables, we also surveyed our staff to get qualitative feedback on the new machinery and equipment.
Our approach to this project was to go wide and not deep, allowing us to test various equipment types. The emissions reductions per equipment we achieved ranged from 20 percent to an impressive 100 percent, depending on the equipment used.
Vehicle specifications
Vehicle comparisons
We achieved a 100 percent reduction in emissions for processes where we employed fully electric machinery thanks to Meta’s commitment to purchasing renewable energy for operations and construction.
The Meta data center construction site incorporates a range of electric and hybrid machinery, including hybrid aerial boom lifts, electric mini-excavators, hybrid excavators, hybrid light towers, electric forklifts, electric utility terrain vehicles, energy storage systems, electric buses, hybrid dozers, and electric telehandlers.
One of our most significant achievements on this project has been using hybrid generators to decrease emissions. These generators work in tandem with batteries or energy storage systems. The tandem approach allows Turner Construction Company to run generators at peak efficiency to charge the batteries, which then power the equipment. This approach has led to substantial emissions reductions across the site.
Q3: What ownership model did you use to employ the hybrid and electric construction equipment? Is it harder to procure electric and hybrid machinery for construction?
Turner Construction Company is the general contractor on the Altoona project for Meta. The company subcontracts the project to various trade partners in addition to self-performing portions of the work themselves. The trade partners employ their machinery, whether rental or company-owned, on the project.
Turner Construction Company went against the status quo for this project and chose an innovative contracting model called the Contractor Controlled Equipment Program. This model put Turner Construction Company, as the general contractor, in more control of the machinery and equipment used on the project. Turner Construction Company connected its trade partners to Sunbelt Rentals and encouraged them to rent hybrid and electric construction equipment parked at a yard on-site. This model also provided for significant (emissions) reduction through reducing the transportation of equipment to the site.
While it is usually harder to procure electric and hybrid machinery as the lead times can be between 12 and 24 months, our partnership model with Sunbelt Rentals allowed us immediate access to the machinery because we offered them full utilization of the machinery through our various trade partners.
Q4: On-road electric vehicles often have higher purchase prices than their conventional counterparts. However, they are generally cheaper to operate and have lower lifetime costs of ownership. How do the costs (purchase price and ongoing operation) of electric and hybrid machinery for construction compare to conventional machinery?
Project managers analyze the following three broad categories of costs to determine the equipment’s suitability for a project: the upfront cost of purchasing or renting the machinery, maintenance costs, and fuel costs.
While the initial purchase or rental cost tends to be higher for electric and hybrid machinery, we have found that the maintenance and fuel costs are lower. This has created many instances where the lower-emissions equipment is already cost-competitive or less expensive. Evaluation of electric or hybrid equipment has to consider the total cost of ownership, not just the upfront purchase price. We expect this to continue to improve as more options come online and the technology progresses.
Rental companies like Sunbelt Rentals calculate the rental rate for machinery based on these costs. However, since electric and hybrid machinery is new and relatively rare, data are scarce to help develop these rates. The Meta project allowed Sunbelt Rentals to collect data on the machinery through telematics. The data collection will enable them to estimate the maintenance costs for running the equipment and develop a competitive rental rate that reflects those costs.
Q5: Besides emissions reduction, what other advantages have you seen with these vehicles and machinery that might attract other construction companies to adopt them?
We have found that electric and hybrid machinery offer numerous benefits beyond greenhouse gas emissions reductions. As I mentioned earlier, these benefits include lower fuel and maintenance costs. These machines are more efficient, and the electricity is cheaper than diesel. The stability of electricity prices, as opposed to volatile fuel prices, also simplifies project management.
The electric equipment can often be diagnosed remotely, which results in a much quicker turnaround for repair and maintenance operations, minimizing costly downtime.
Electric equipment and vehicles are also quieter, have low or no tailpipe emissions that cause air pollution, and have minimal fuel and lubricant spillage risk. These factors improve on-site working conditions by reducing air pollutants that workers breathe in and are exposed to.
Q6: What do construction workers think about operating these vehicles and machinery? Do they like it, or do they resist using them?
Some of our workers were initially hesitant to try out a brand-new technology. However, as they spent more time operating electric and hybrid machinery, they became increasingly comfortable with them. Given the choice, most operators now prefer electric and hybrid models. The workers also shared that the reduced vibrations contribute to reduced fatigue at the end of a workday.
Q7: Heavy-duty construction equipment draws significant power, regardless of the fuel type. For the electric models, what challenges have you experienced, if any, in procuring the power to charge the vehicles and machinery?
The Meta data center project had an advantage as much of the campus was already operational, with significant power infrastructure. However, power supply can be a challenge at construction sites, especially if construction equipment power requirements exceed what the building will eventually need. The lead time for ordering utility equipment to energize a worksite can be 12-18 months. It requires significant planning and conversations with utilities ahead of time to break ground on time.
Turner Construction Company has explored on-site renewable energy generation solutions for such sites, including off-grid solar panels and mobile solar units linked to batteries. During design, many projects do an energy model for what the permanent building will require. We have begun to roll out a similar service for the construction phase, allowing us to get extremely detailed on what will be required from the utility and by when. All project stakeholders need to come together early to start energy procurement during the site selection process.
Q8: Are there any other challenges with hybrid and electric construction equipment that you’d like to highlight?
While momentum is quickly building in this important area, construction companies and trade partners who choose to make their operations more environmentally sustainable face several challenges. This includes limited machinery and equipment options on the market, which can result in 12-24 month lead times for electric models to reach construction sites.
Ensuring a stable power supply on dynamic and large construction sites can also be challenging. The machinery and equipment can move around the site over the course of the project. The distribution grid may not always have the flexibility to move with the machinery and equipment.
Additionally, overcoming negative perceptions about new technology within the construction industry requires education and time. There is skepticism about the practicality of incorporating equipment that may see significant decreases in runtime during the winter. This issue is linked to our sites’ lack of mobility of electric power sources.
Increased distance from a power source combined with decreased runtime for the machinery and equipment can significantly increase the downtime and make some electric and hybrid machinery and equipment less viable options for some projects.
Q9: In recent years, we have seen a significant push from governments to increase electric vehicle adoption, with policy measures including rebates for consumers, incentives for charging equipment manufacturers and site hosts, and setting sales targets. What kind of policy support does the construction industry require for hybrid and electric construction equipment to become mainstream?
City and local governments have a role in leveling the playing field for hybrid and electric construction equipment. Requiring lifecycle assessments (of emissions), which include construction, for buildings encourages building owners and developers to consider cleaner construction options.
Some local governments have started mandating emission-free construction. The C40 global network of cities introduced a Clean Construction Declaration, signed by five forward-thinking members of the C40 network: Budapest, Los Angeles, Oslo, Mexico City, and San Francisco.
The cities have pledged to take action and enact policies and regulations to require zero-emission construction machinery in municipal projects by 2025 and zero-emission construction sites citywide by 2030, where available. They aim to reduce embodied emissions by at least 50 percent for all new buildings and infrastructure projects by 2030.
Q10: Is there anything you would like to share with project managers who are considering piloting hybrid and electric construction equipment?
Project managers considering the adoption of hybrid and electric construction equipment should start by exploring all available hybrid and electric options and then evaluate the feasibility of each equipment and process. It makes sense to start with low-risk, small, and cost-neutral equipment and gradually expand the usage of new low- or no-emission equipment and processes.
They should also contact their utilities early in the process so they have power supplied to their sites ahead of time. Hybrid microgrids that combine solar energy with on-site battery storage and generators may help cover power gaps for some projects if the energy demand from a project exceeds the grid’s capacity.
Turner Construction Company builds partnerships with original equipment manufacturers and offers its sites as testing grounds for new machinery, facilitating the creation of case studies and fostering collaboration within the industry.
Other construction companies that want to implement electric and hybrid construction projects should also collaborate with original equipment manufacturers and rental companies and allow testing on their sites.
Partnerships and collaboration across the nascent electric and hybrid construction industry are vital for the success of this industry and the widespread adoption of these machines and practices.
Conclusion
Policy makers, utilities, original equipment manufacturers, and construction companies will play a vital role in accelerating the adoption of hybrid and electric construction equipment. The construction industry is at a crucial juncture where a collaborative effort toward electrification can lead to cleaner and quieter job sites with reduced emissions while significantly reducing costs for construction companies.
Stay tuned for more in this series as we explore electrification efforts in other off-road vehicles and industries, paving the way for a more sustainable future.