Spotlight on Off-Road Transportation Electrification: Q&A on Minnesota Power’s Mine Truck Electrification Project
September 20, 2024 | M. Moaz Uddin | Education
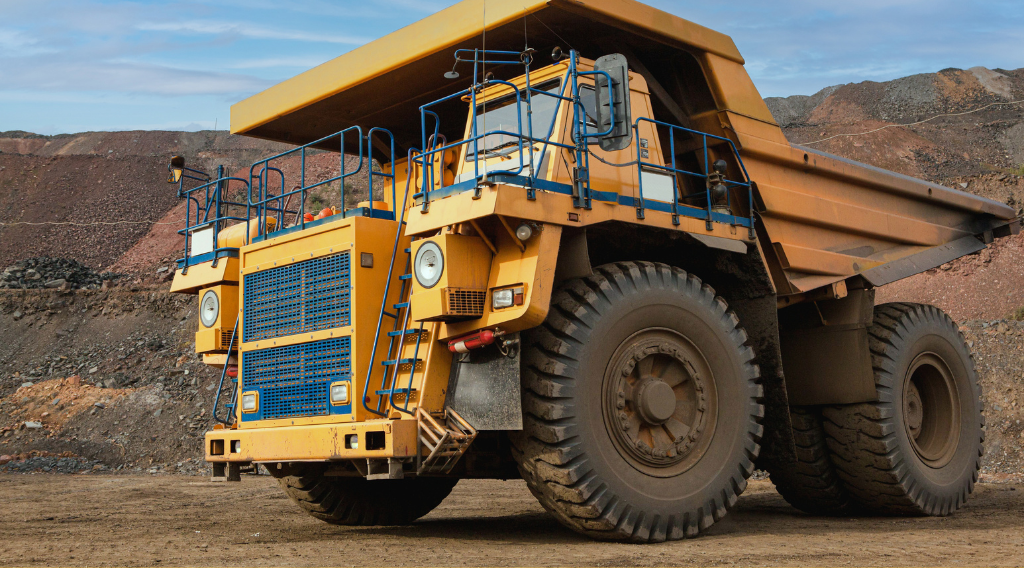
While we often hear about the electrification of passenger vehicle fleets and, more recently, commercial vehicle fleets, off-road transportation is often sidelined in these conversations. This post is part of a series that will spotlight electrification efforts for off-road vehicles, which include equipment and machinery used in construction, mining, agriculture, and ports.
This post will focus on the mining industry, which contributes between 4 and 7 percent of greenhouse gas emissions globally due to its heavy reliance on fossil fuels. Electrifying mining vehicles and equipment can significantly cut the industry’s emissions by eliminating exhaust gases, improving energy efficiency, and using renewably sourced energy as fuel for mining trucks and other equipment.
This post highlights Minnesota Power’s plans to introduce electric mining trucks, also known as e-trolley systems, to mines in their service territory.
ALLETE is a leading energy company headquartered in Duluth, Minnesota. ALLETE’s largest business unit, Minnesota Power, is an electric utility that serves over 150,000 customers, 14 municipalities, and some of the nation’s largest industrial customers. Other businesses include ALLETE Clean Energy, BNI Energy, Superior Water, Light and Power, ALLETE Renewable Resources, and New Energy Equity. ALLETE also has 8 percent ownership of American Transmission Company.
Dave Chura, Manager – Government Funding, Contract Compliance at ALLETE, spoke to Drive Electric Minnesota about the company’s move toward making mining in Minnesota more sustainable.
Q1: Tell us about Minnesota Power’s mine truck electrification project. How did this project come about, and what are the major milestones you have achieved?
Through our EnergyForward plan, we have transformed our energy supply to be over 50 percent renewable, which helps our mining companies reduce the environmental footprint for minerals and metals used in the clean energy economy.
Mine truck electrification creates the potential for all of Minnesota to realize the benefits of electrification at an industrial scale and for mining companies to advance their carbon-free operational goals.
We partnered with a local mine, truck manufacturer, and engineering firm to develop a pilot project to demonstrate the emission reductions and productivity gains from electrifying mining trucks. The analysis was site-specific and modeled the trolley infrastructure and truck needs along with the diesel fuel and emission reductions. The modeling also evaluated productivity gains.
The evaluation revealed the following key findings:
- Diesel fuel consumption on the trolley line section is reduced by over 95 percent—that is a reduction of over 4 million gallons of diesel annually.
- The reduction in diesel fuel use results in a decrease of more than 14,000 metric tons of CO2 (carbon dioxide). That is a significant reduction of emission and criteria pollutants in an area of our state that is near key Class 1 airsheds, such as the Boundary Waters Canoe Area Wilderness, Voyageurs National Park, and several Minnesota Pollution Control Agency-defined areas of environmental justice.
- Mine truck electrification has the added ability to enable additional interruptible electric load, which can react quickly in response to the variable output from renewable generation, thus helping to integrate renewable energy further while keeping costs down for customers.
In 2023, we were successful in getting legislation introduced at the Minnesota Legislature to provide $10 million in funding for a mine truck demonstration project. Unfortunately, the funding was not included in the final appropriations that session. Minnesota Power has also met with the White House, the US Department of Energy (DOE), and Minnesota’s congressional delegation to discuss the opportunity.
In April 2023, we submitted a concept paper in response to a DOE Industrial Decarbonization funding opportunity for a demonstration project, which would be the first implementation of e-trolley in a mine in the United States with significant opportunity to expand to other mine locations locally and across the United States. The proposal was not selected for funding, but Minnesota Power continues to look for additional state and federal funding opportunities to support mine truck electrification.
Q2: How do conventional and electric mining trucks’ equipment and infrastructure requirements vary?
Traditional diesel-mechanical trucks are the decades-old mine truck configuration utilizing conventional diesel engines to propel the trucks.
Electric drive trucks are a more contemporary mine truck configuration utilizing a diesel generator to convert diesel fuel to mechanical energy used to power the truck’s drive wheel electric motors, similar to the technology used on diesel locomotives.
Electric drive-on trolley assist is like the electric drive mine truck but with the addition of a supplemental external electric power supply delivered to the mine truck by an overhead trolley system for a portion of the truck’s haul route, significantly reducing diesel fuel consumption, replacing it by remotely generated electric power.
Electric drive-on trolley mine trucks require the installation of a pantograph on top of the truck and the trolley line infrastructure along its route, similar to traditional trolley cars found in some US cities. A pantograph installed on the mine truck raises and lowers as needed to connect electrical contacts on the mine truck to overhead power lines. When connected, electric power is relayed to the electric motors on the truck to power the truck’s drive wheels. The truck’s diesel engine disengages and idles until it is needed again when the truck departs from the trolley system.
Q3: Can you tell us about the upfront infrastructure costs of the trolley line infrastructure?
In 2023, the cost for the trolley line infrastructure was estimated to be $5-6 million per mile. However, the costs and benefits can vary greatly and are highly site-specific. Factors influencing costs include the slope, length, and life of the haul road, the price of diesel, and the condition of the existing truck fleet at a mine.
Q4: On-road electric vehicles often have higher purchase prices than their conventional counterparts. However, they are generally cheaper to operate and have lower lifetime ownership costs. How do electric mining truck costs (purchase price and ongoing operation) compare to conventional trucks?
Electric drive trucks are initially more expensive than traditional diesel-mechanical trucks, but they consume less diesel fuel and have lower maintenance costs. Additionally, mine trucks operating on trolley lines are more productive, and, in some cases, that allows a mining company to purchase and operate fewer trucks.
Q5: Have you estimated the emissions reductions when switching from conventional to electric mining trucks? How might the emission reductions vary from project to project?
The emission reductions will vary depending on site-specific conditions. In our site-specific analysis, adding trolley assist to Tier IV mine trucks reduces CO2 by 14,359 metric tons when supplied with 100 percent carbon-free electricity. This is equal to the emissions reduction from electrifying 3,122 gasoline passenger vehicles.
Minnesota Power has conducted desktop modeling evaluating two model mines—a small mining operation and a large mining operation, based on an average of site characteristics from the six operating iron ore mines in Minnesota. Even in the small mining operation analysis, electrification reduced CO2 emissions by more than 7,600 metric tons.
Q6: How do electric mining trucks perform in their duty cycles compared to their conventional counterparts?
As demonstrated in this video, electric trucks on trolley can travel up to two times faster than conventional trucks, which increases productivity and can allow for fewer trucks in the mining company’s fleet.
Q7: What do drivers and other workers think about operating these vehicles?
Electric trucks improve the work environment for drivers due to lower noise during operation and reduced need for maintenance. For these reasons, the United Steelworkers testified in support of the electric mine truck demonstration project funding at the Minnesota Legislature in 2023.
Q8: Heavy-duty mining trucks draw significant power, regardless of the fuel type. What challenges do you expect with electric models, if any, when powering vehicles?
It is crucial to maintain the haul road surface to ensure the appropriate distance between the road and the trolley line so the truck remains in contact with the line along the trolley route. If a truck gets ejected from the line due to an uneven road surface, it can attempt to reconnect or continue along the way under diesel power. Trolley-assist projects are operating successfully around the world in climates similar to Minnesota (e.g., Finland, Sweden, and Canada).
Q9: Could you talk to us about the opportunity Minnesota Power sees in implementing the e-trolley system in Minnesota?
This would be the first implementation of an e-trolley in a mine in the United States, with a significant opportunity to expand to other mine locations locally and across the United States. Minnesota is home to six taconite mines, which produce 80 percent of the nation’s iron ore pellets. Mine truck electrification provides the opportunity for significant emission reductions, resulting in even cleaner pellets.
Q10: In recent years, we have seen a significant push from governments to increase electric vehicle adoption, with policy measures including rebates for consumers, incentives for charging equipment manufacturers and site hosts, and setting sales targets. What kind of policy support does the mining industry require for electric mining trucks to become mainstream?
State and federal support is needed to help offset some of the economic challenges given lower priced fuel and flatter haul grades in Minnesota than exist in other locations where trolley-assist operations are in place today. The greatest emissions and fuel reductions from electric mine trucks are achieved in mines that have steep haul grades. More expensive diesel also results in higher fuel savings from switching to e-trolley systems.
The federal government and states have helped incentivize residential and commercial electric vehicles, resulting in significant environmental and economic benefits. Their support for this project would achieve the benefits of electrification at an industrial scale.
Q11: Is there anything you would like to share with mining companies and utilities who are considering piloting electric mining trucks?
We consider mine truck electrification a fantastic opportunity for both Minnesota Power and the mines to achieve carbon reduction commitments and advance the clean energy transition. Steel is a critical component in the continued development of clean energy and technologies to reduce America’s carbon footprint.
While the American steel industry is the cleanest and most energy-efficient of the seven largest steel-producing countries in the world, mine truck electrification allows the industry to produce greener steel than it already does. Electric mine trucks can bring similar benefits to other industries in the mining sector that want to achieve their carbon reduction goals.
Conclusion
The electrification of mine trucks represents a transformative step toward a more sustainable mining industry. Minnesota Power’s initiative to introduce e-trolley systems underscores the potential for significant environmental benefits, including substantial reductions in diesel fuel consumption and greenhouse gas emissions in the mining industry.
While challenges in funding these projects remain, pilot projects like the one carried out by Minnesota Power highlight the numerous benefits of electrifying mine trucks, such as improved productivity, better working conditions, and enhanced environmental stewardship.
With continued support from federal and state entities in the form of programs like the Environmental Protection Agency’s Diesel Emissions Reduction Act (DERA) program and the Minnesota Pollution Control Agency’s Volkswagen Settlement Grants, pioneering projects like the one highlighted in this post can set a precedent for electrification in off-road transportation.
You can learn more about Minnesota Power’s transportation electrification work and sign up for updates about the company’s electric vehicle programs on the company’s website.
Stay tuned for more in this series as we explore electrification efforts in other off-road vehicles and industries, paving the way for a more sustainable future. We covered electric construction equipment in our previous blog post.